Laser Welding: The Future of Precision Joining Technology
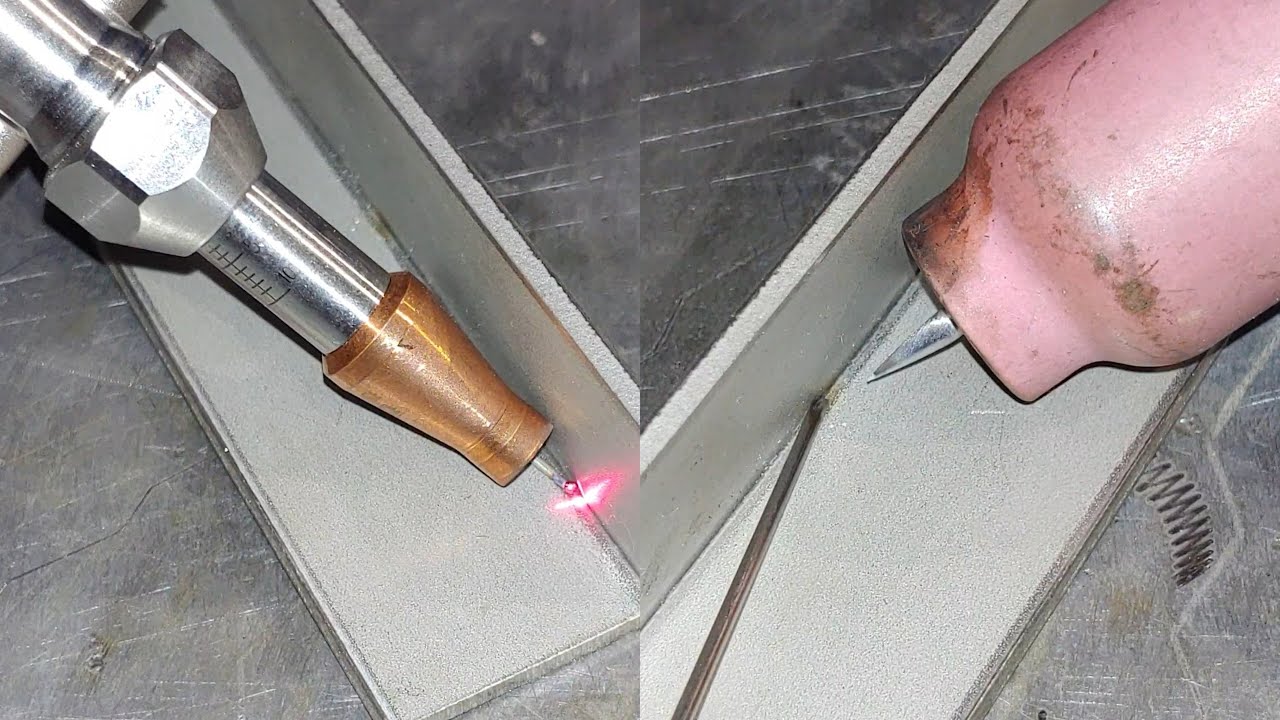
In the vast and ever-evolving landscape of manufacturing and repair, one technique stands out for its precision, efficiency, and versatility: laser welding. This modern method uses laser beams to join various materials, including metals and plastics, in a way that was once unimaginable. The process offers a multitude of advantages over traditional welding techniques, making it a cornerstone in the fields of automotive, aerospace, medical device manufacturing, and many more. This post delves into the intricacies of laser welding, exploring its process, types, benefits, applications, and the future prospects of this cutting-edge technology.
The Essence of Laser Welding
At its core, laser welding is a process that employs a concentrated beam of light to melt and fuse materials together. The laser beam provides a focused heat source, allowing for narrow, deep welds and high welding rates. The process is highly controllable and can be precisely targeted, which minimizes the heat-affected zone (HAZ) and reduces distortion and warping of the parts being welded.
Types of Laser Welding
There are primarily two types of laser welding: conduction limited welding and keyhole welding. Conduction-limited welding occurs when the laser beam heats the surface of the material, and the heat is conducted downwards to create the weld. This method is suitable for thin materials and results in smooth weld surfaces. On the other hand, keyhole welding involves the creation of a vapor cavity (the keyhole) by the laser’s intense focus, which penetrates through the entire thickness of the material, allowing for the welding of thicker materials.
Advantages of Laser Welding
The benefits of laser welding are numerous, making it an attractive option for many industries. Some of the key advantages include:
- Precision and Control: The ability to focus the laser beam precisely allows for intricate welds on small or complex parts.
- Minimal Heat Input: This reduces the HAZ and distortion of the parts being welded, preserving the mechanical and physical properties of the materials.
- High Speed: Laser welding is faster than conventional welding methods, significantly increasing productivity.
- Versatility: It can be used to weld a wide range of materials, including dissimilar metals.
- Automation: The process can be easily automated, integrated with robots, and controlled by computer programming, enhancing consistency and reducing labor costs.
Applications of Laser Welding
Laser welding’s versatility makes it suitable for a wide array of applications across various industries:
- Automotive Industry: Used for welding components like transmission components, airbag initiators, and battery packs for electric vehicles.
- Aerospace: Essential for welding critical components that require precision and strength, such as engine parts and structural components.
- Medical Devices: Utilized for joining small parts in surgical instruments and implants, where precision and reliability are paramount.
- Electronics: Applied in the micro-welding of connectors, sensors, and other components, where traditional welding techniques might cause damage.
Overcoming Challenges
Despite its many advantages, laser welding is not without its challenges. The initial setup and equipment costs can be high, making it a significant investment. Additionally, the process requires skilled operators and technicians to manage and maintain the sophisticated equipment. However, the return on investment through increased productivity, reduced waste, and improved product quality often outweigh these initial challenges.
The Future of Laser Welding
As technology advances, laser welding is set to become even more efficient and versatile. Developments in fiber laser technology are making laser welders more compact, energy-efficient, and powerful. Innovations such as real-time monitoring and control systems are enhancing the quality and consistency of welds. Furthermore, the advent of artificial intelligence and machine learning in manufacturing processes promises to optimize laser welding parameters for different materials and applications automatically.
Conclusion
Laser welding represents a significant leap forward in joining technology. Its precision, efficiency, and versatility make it a valuable tool in numerous fields, from automotive to medical devices. Despite its challenges, the ongoing advancements in laser technology and automation are poised to expand its applications and accessibility. As industries continue to demand higher quality and more complex components, laser welding will undoubtedly play a crucial role in meeting those needs, solidifying its position as a key technology in modern manufacturing and repair.