Insert Molding Innovations: Advancing Aerospace and Defense Manufacturing
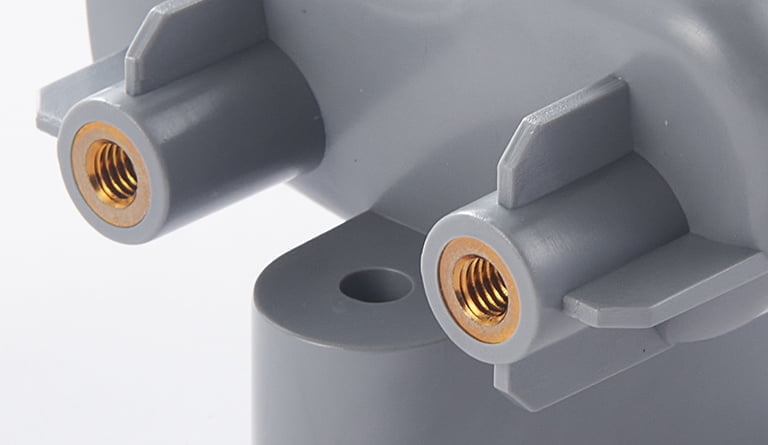
In the dynamic fields of aerospace and defense manufacturing, innovation is a driving force behind progress. Insert molding, a versatile and efficient manufacturing process, has emerged as a key technology in advancing the production of components and parts for aerospace and defense applications. By seamlessly integrating pre-formed components (inserts) into molded parts, insert molding offers unique advantages that enhance efficiency, reduce weight, and improve performance in critical aerospace and defense systems. In this article, we will explore the innovative applications of insert molding in aerospace and defense manufacturing, its benefits, challenges, and future prospects.
Introduction to Insert Molding
Insert molding is a specialized manufacturing process that combines injection molding with the integration of pre-formed components (inserts) to create a single, integrated part. The process involves placing inserts into the mold cavity before injecting molten material, typically a thermoplastic resin, around them. Once cooled and solidified, the molded material forms a seamless, durable part with the inserts securely embedded within. This technique enables the creation of complex geometries, multi-material structures, and functional components with high precision and repeatability, making it well-suited for aerospace and defense applications.
Innovations in Aerospace and Defense Manufacturing
Weight Reduction and Performance Enhancement
Insert molding enables manufacturers to create lightweight, yet structurally robust components for aerospace and defense systems. By integrating high-strength inserts within molded parts, insert molding enhances structural integrity, reduces weight, and improves overall performance in critical applications such as aircraft structures, missile components, and satellite systems.
Complex Geometries and Integration of Functional Features
Insert molding allows for the creation of complex, multi-material parts with integrated functionality, such as encapsulating electronics, sensors, or reinforcement structures within molded housings. This enables the development of innovative aerospace and defense systems with reduced part count, simplified assembly, and improved reliability in harsh operating environments.
Cost Efficiency and Production Optimization
Insert molding streamlines production processes and reduces manufacturing costs by consolidating multiple manufacturing steps into a single operation. By eliminating the need for separate assembly steps, insert molding reduces labor costs, material waste, and production time, making it a cost-effective solution for aerospace and defense manufacturers.
Material Innovation and Customization
Advances in material science and additive manufacturing technologies have expanded the range of materials and customization options available for insert molding in aerospace and defense applications. Manufacturers can now choose from a wide variety of materials, including high-performance polymers, composites, and metal alloys, to meet the specific requirements of each application while optimizing performance and durability.
Quality Assurance and Reliability
Insert molding processes incorporate rigorous quality assurance measures to ensure consistent part quality, dimensional accuracy, and reliability in aerospace and defense systems. By performing regular inspections, dimensional checks, and functional tests, manufacturers can detect defects early and ensure compliance with stringent industry standards and regulatory requirements.
Benefits of Insert Molding in Aerospace and Defense Manufacturing
Enhanced Structural Integrity: Insert molding enhances the structural integrity of components by securely embedding inserts within molded parts, providing mechanical reinforcement and protection against impact, vibration, and thermal stress in aerospace and defense systems.
Weight Reduction: By creating lightweight components with high-strength inserts, insert molding contributes to weight reduction in aerospace and defense systems, improving fuel efficiency, payload capacity, and overall performance.
Improved Functionality: Insert molding enables the integration of functional features, such as electronic circuits, sensors, or reinforcement structures, within molded parts, enhancing the functionality and performance of aerospace and defense systems in diverse operating conditions.
Streamlined Production: Insert molding streamlines production processes by consolidating multiple manufacturing steps into a single operation, reducing labor costs, material waste, and production time while maintaining high part quality and reliability.
Customization and Innovation: Insert molding offers designers greater flexibility to create customized components with innovative designs and advanced materials, optimizing performance and durability in aerospace and defense applications.
Challenges and Considerations
Material Selection: Selecting the appropriate materials for insert molding in aerospace and defense applications requires careful consideration of factors such as mechanical properties, thermal stability, chemical resistance, and compatibility with inserts and operating environments.
Design Complexity: Designing complex geometries and integrating functional features within molded parts may present challenges in tooling design, mold fabrication, and production optimization, requiring close collaboration between designers, engineers, and manufacturers.
Quality Assurance: Maintaining consistent part quality and dimensional accuracy in insert molding processes requires rigorous quality assurance measures, including regular inspections, dimensional checks, and functional tests, to ensure compliance with industry standards and regulatory requirements.
Cost-Benefit Analysis: While insert molding offers numerous benefits in aerospace and defense manufacturing, including weight reduction, performance enhancement, and production optimization, manufacturers must conduct a thorough cost-benefit analysis to assess the economic viability and return on investment of implementing insert molding processes.
Future Prospects and Innovations
Additive Manufacturing Integration
The integration of additive manufacturing technologies such as 3D printing with insert molding processes is enabling the creation of highly customized, complex parts with reduced lead times and tooling costs, further advancing innovation in aerospace and defense manufacturing.
Smart Manufacturing Technologies
The adoption of smart manufacturing technologies such as automation, robotics, and data analytics is transforming production processes and supply chains in aerospace and defense manufacturing, enabling greater efficiency, flexibility, and quality control.
Advanced Materials and Composites
Advances in material science, including the development of high-performance polymers, composites, and metal alloys, are expanding the range of materials available for insert molding in aerospace and defense applications, offering enhanced performance and durability in diverse operating environments.
Sustainability and Environmental Stewardship
Aerospace and defense manufacturers are increasingly embracing sustainability and environmental stewardship principles, including the use of recycled materials, bio-based resins, and closed-loop systems in insert molding processes to minimize waste and reduce environmental impact.
Conclusion
In conclusion, insert molding is driving innovation in aerospace and defense manufacturing by enabling the creation of lightweight, structurally robust components with integrated functionality and improved performance. By seamlessly integrating pre-formed inserts within molded parts, insert molding streamlines production processes, reduces manufacturing costs, and enhances reliability in critical aerospace and defense systems. While challenges such as material selection, design complexity, and quality assurance remain, ongoing advancements in technology, materials, and processes are paving the way for further innovation and progress in insert molding for aerospace and defense applications. As manufacturers continue to leverage the benefits of insert molding, the future of aerospace and defense manufacturing looks poised for continued growth and advancement.