The Science Behind Insert Molding: Understanding Materials Integration
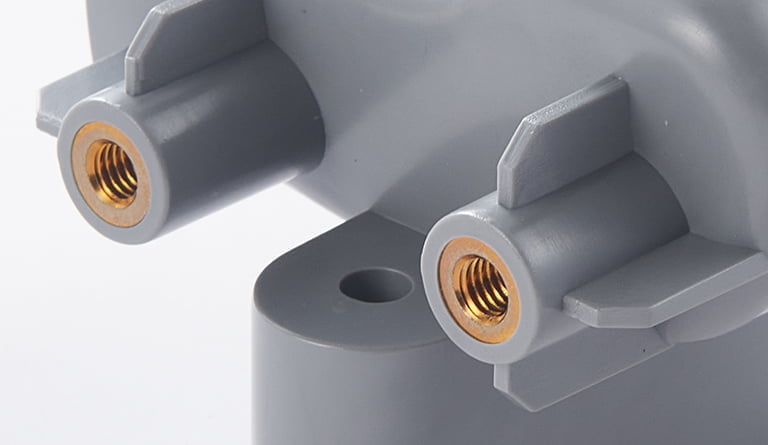
In the realm of modern manufacturing, where innovation and efficiency are paramount, insert molding stands out as a powerful technique for creating complex, multi-material components. At the heart of insert molding lies the intricate science of materials integration, which involves seamlessly combining diverse materials to achieve superior performance, durability, and functionality. This article explores the science behind insert molding, delving into the principles of materials integration, the challenges it presents, and the strategies for optimizing the process to achieve optimal results.
Understanding Insert Molding
Insert molding is a specialized form of injection molding that involves encapsulating pre-formed components, known as inserts, within a molded part. These inserts can be made from various materials, including metals, plastics, ceramics, and electronic components. The process typically begins with the placement of inserts into the mold cavity, followed by the injection of molten material, usually a thermoplastic resin. As the molten material cools and solidifies, it forms a cohesive bond with the inserts, creating a single, integrated part.
The Science of Materials Integration
Materials integration lies at the core of insert molding, as it involves combining different materials to achieve desired performance characteristics. Several key principles govern the science of materials integration in insert molding:
Material Compatibility: Selecting materials that are compatible with each other is essential for achieving successful materials integration. Compatibility encompasses factors such as thermal expansion coefficients, adhesion properties, and chemical interactions between materials. Incompatibility can lead to bonding issues, material degradation, or dimensional instability, compromising the quality and performance of the final part.
Bonding Mechanisms: The bonding between materials in insert molding occurs through mechanical interlocking, chemical bonding, or a combination of both. Mechanical interlocking occurs when the molten material flows around the inserts and solidifies, creating a physical bond. Chemical bonding occurs when the molten material chemically reacts with the surface of the inserts, forming strong molecular bonds. Understanding the bonding mechanisms is crucial for optimizing insert molding processes and achieving robust part quality.
Material Properties: The properties of the materials used in insert molding, such as mechanical strength, thermal conductivity, and electrical conductivity, play a critical role in determining the performance of the final part. By carefully selecting materials with complementary properties, manufacturers can enhance the functionality, durability, and reliability of insert-molded components.
Process Parameters: The injection molding process parameters, including temperature, pressure, injection speed, and cooling rate, influence the materials integration process and the properties of the final part. Optimal process parameters are determined based on material properties, part geometry, and production requirements. Fine-tuning these parameters is essential for achieving uniform material distribution, minimizing defects, and ensuring part quality consistency.
Challenges in Materials Integration
While materials integration offers numerous benefits, it also presents several challenges that must be addressed to achieve successful outcomes in insert molding:
Material Mismatch: Mismatched material properties, such as differences in thermal expansion coefficients or melt temperatures, can lead to bonding issues and dimensional instability in insert-molded parts. Careful material selection and process optimization are required to mitigate these challenges and ensure robust materials integration.
Surface Preparation: Proper surface preparation of inserts is essential for promoting adhesion and bonding between materials in insert molding. Surface treatments, such as cleaning, etching, or priming, may be necessary to remove contaminants and promote bonding. Inadequate surface preparation can result in poor adhesion and compromised part quality.
Insert Placement: Accurate and precise placement of inserts within the mold cavity is critical for achieving uniform material distribution and bonding in insert molding. Improper insert placement can lead to voids, misalignment, or incomplete encapsulation, affecting part integrity and functionality. Automated insert placement systems and precise mold designs are employed to ensure consistent insert positioning and alignment.
Optimization of Process Parameters: Achieving optimal process parameters is crucial for controlling material flow, minimizing defects, and achieving uniform part quality in insert molding. Process optimization requires careful experimentation and analysis to determine the ideal combination of temperature, pressure, injection speed, and cooling rate for each specific application.
Strategies for Optimizing Materials Integration in Insert Molding
To overcome the challenges associated with materials integration in insert molding and achieve optimal results, manufacturers can employ several strategies:
Comprehensive Material Selection: Conduct thorough material compatibility studies and select materials with complementary properties to ensure successful materials integration. Consider factors such as melt temperatures, adhesion properties, and chemical compatibility when choosing materials for insert molding applications.
Surface Treatment Techniques: Implement effective surface treatment techniques, such as cleaning, plasma treatment, or chemical priming, to prepare inserts for optimal bonding in insert molding. Proper surface preparation is essential for promoting adhesion and enhancing part quality.
Precision Mold Design: Design molds with precision to facilitate uniform material flow, proper venting, and accurate insert positioning in insert molding. Incorporate features such as inserts guides, gating systems, and cooling channels to optimize part quality and dimensional stability.
Advanced Process Control: Utilize advanced process control technologies, such as real-time monitoring systems and automated feedback loops, to optimize process parameters and ensure consistent part quality in insert molding. Continuous process monitoring and adjustment help minimize defects, reduce scrap, and improve production efficiency.
Applications of Materials Integration in Insert Molding
Materials integration in insert molding finds applications across various industries and products, including:
- Automotive components (e.g., sensors, connectors, interior trim)
- Electronics (e.g., circuit boards, connectors, housings)
- Medical devices (e.g., catheters, surgical instruments, drug delivery systems)
- Aerospace and defense (e.g., avionics housings, UAV components)
- Consumer goods (e.g., appliance components, electronic enclosures, sporting equipment)
Conclusion
In conclusion, the science of materials integration plays a critical role in the success of insert molding processes. By understanding the principles of materials compatibility, bonding mechanisms, and process optimization, manufacturers can achieve robust materials integration and produce high-quality insert-molded components with enhanced performance and durability. Addressing challenges such as material mismatch, surface preparation, insert placement, and process optimization requires careful consideration and strategic implementation of advanced techniques and technologies. By leveraging the science of materials integration, manufacturers can unlock the full potential of insert molding and drive innovation across diverse industries and applications.